About Us
We help middle-market organizations achieve breakthrough performance.
Our Values
Our values are built on a foundation of integrity, respect, and excellence. We believe in delivering high-quality services that meet the unique needs of each client, and we are committed to building lasting relationships based on trust and mutual respect.
Our Mission
Our mission is to help organizations achieve operational excellence and sustainable growth through the implementation of continuous improvement methodologies. We are committed to delivering measurable results and adding value to our clients' businesses.
Our Vision
Our vision is to become the leading continuous improvement consulting firm in Arizona, known for delivering innovative solutions that drive transformational change and help organizations achieve their strategic goals.
Our Services
Sonoita Equity Partners offers a comprehensive range of services designed to help clients identify and achieve their goals allowing them to staying ahead of the competition. Services include:
Process improvement, where we analyze a business’s existing processes and identify opportunities to streamline and optimize them for greater efficiency and cost savings.
Custom framework development, where we work with stakeholders to develop a tailored solution that meets an organization’s specific needs and addresses any unique challenges.
Strategy and innovation services, where we help develop a clear and effective strategy that positions any organization for long-term success.
We help organizations innovate and stay ahead of the curve with the latest trends and technologies. Our experienced team of consultants works closely with the client every step of the way to ensure that our services are aligned with their goals and deliver measurable results.
Lean is a process of continuous improvement techniques and activities to go beyond the symptom of a problem, identify a root cause, and take action to close the gaps.
Our Approach
Our approach applies the core principles of Lean, which revolve around identifying and eliminating non-value-added activities, reducing waste, optimizing processes, and continuously improving performance. When there is a roadblock or challenge that a business is facing lean methodologies can be applied to resolve those challenges. The application of the following key concepts can help any organization regardless of industry or size release trapped value:
Outcome-Focus: Lean emphasizes understanding value from the customer's perspective. Value refers to any action, process, or feature that meets the customer's needs and requirements.
Value Stream: The value stream represents the end-to-end flow of activities required to deliver a product or service to the customer. It includes all steps, resources, and processes involved, from raw materials to the final delivery.
Waste (Muda, Mura, Muri) Reduction: Waste refers to any activity or process that does not add value to the customer. Lean identifies several types of waste, such as overproduction, waiting, unnecessary transportation, excess inventory, defects, and unnecessary motion.
Just-in-Time (JIT): JIT is a key Lean concept that aims to deliver the right product or service, at the right time, in the right quantity. It involves eliminating unnecessary inventory and ensuring that work or materials flow through the system precisely when they are needed.
Continuous Improvement (Kaizen): Lean promotes a culture of continuous improvement, where small incremental changes are encouraged to optimize processes, eliminate waste, and enhance efficiency. This involves empowering employees to identify and address problems and inefficiencies in their work areas.
Respect for People: Lean emphasizes the importance of respecting and engaging people at all levels of the organization. It recognizes that employees are a valuable source of knowledge and ideas for improvement, and their involvement is crucial to achieving Lean objectives.
Visual Management: Lean promotes the use of visual tools and techniques to make information, processes, and performance visible and easily understood. Visual management helps teams monitor progress, identify issues, and collaborate effectively.
Lean is a powerful methodology for continuous improvement that can be applied to manufacturing, government and service industries. By focusing on customer value, optimizing processes, reducing waste, and fostering a culture of continuous improvement, organizations can release trapped value and achieve higher levels of efficiency and customer satisfaction. Embracing Lean principles such as outcome-focused approach, value stream mapping, waste reduction, just-in-time delivery, continuous improvement, respect for people, and visual management can enable organizations to drive positive change, enhance performance, and sustain success in today's competitive business landscape.
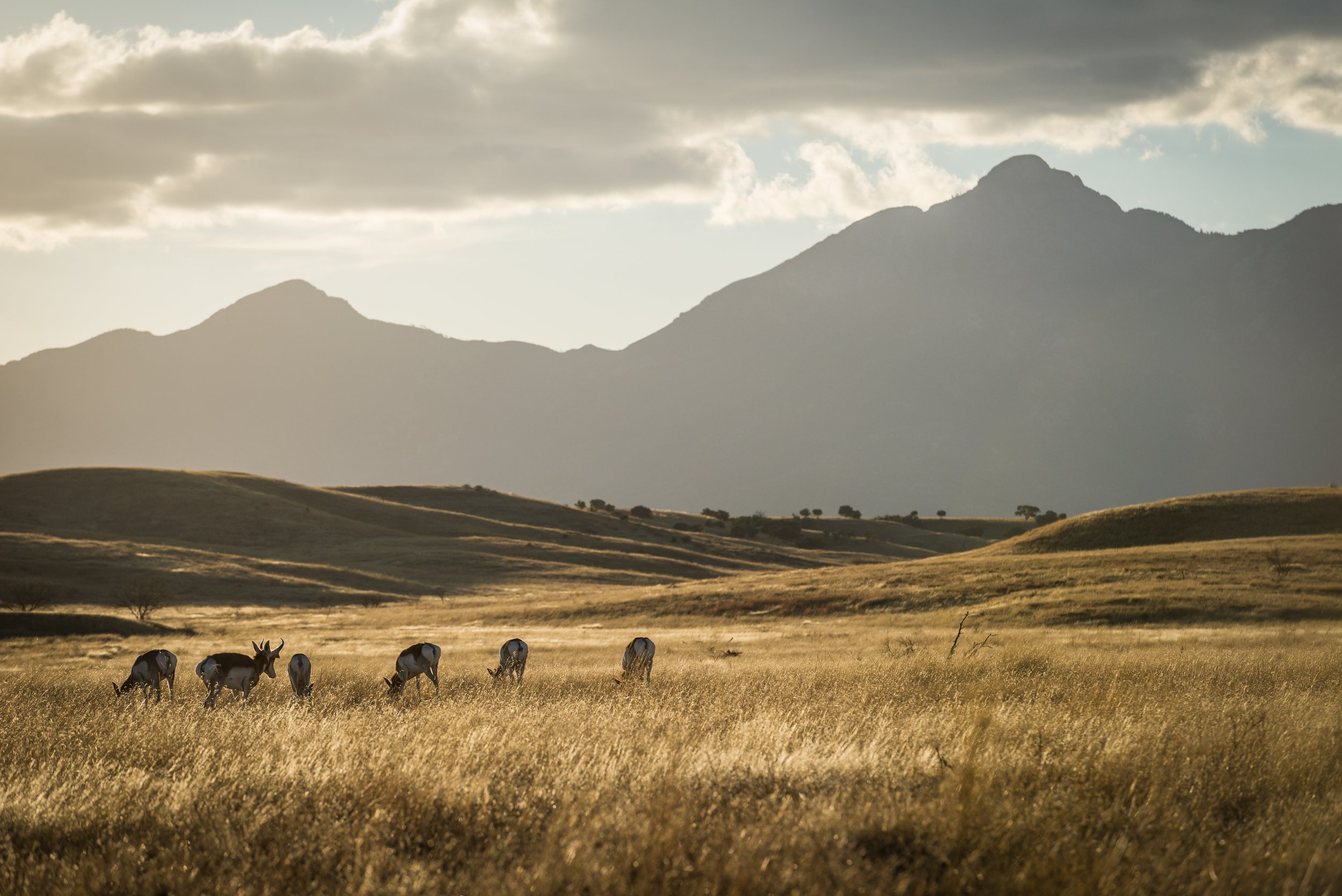